1、净化材料的管理(添加催化剂、纯碱)
1. Management of purification materials (adding catalysts, soda ash)
催化剂的添加需要按照添加的规程进行,要活化3-4小时,并且要做到缓慢均匀滴加的脱硫系统内,其原因就是为了保持脱硫液的氧化能力均匀,防止出现过氧化或氧化能力不足的状况。同理纯碱的加入也需要均匀补加,防止引起脱硫液PH和碱度的波动,导致副盐增长速率加快。在净化材料的添加上也出现过没有按照规定的数量进行添加的情况,这给工艺管理人员造成误导。
The addition of catalysts needs to be carried out according to the addition procedures, activated for 3-4 hours, and slowly and uniformly added in the desulfurization system. The reason is to maintain the uniform oxidation ability of the desulfurization liquid and prevent peroxidation or insufficient oxidation ability. Similarly, the addition of pure alkali also needs to be evenly added to prevent fluctuations in the pH and alkalinity of the desulfurization solution, leading to an accelerated growth rate of secondary salts. There have also been cases of not adding the required amount of purification materials, which has misled process management personnel.
其实这些操作要求许多管理人员和现场的操作人员都明白,但在执行上却没有严格地按照规程的要求去做,或根本没有按规程的要求去做,这就出现了截然不同的运行效果。这就是管理出了问题。
In fact, many managers and on-site operators are required to understand these operations, but they have not strictly followed the requirements of the regulations in execution, or have not followed the requirements of the regulations at all, resulting in completely different operational effects. This is when there is a problem with management.
许多企业忽视了这方面的管理,认为只要添加的总数量不变,副盐的增长速率与添加方式没有太大关系,甚至有的企业通过突击加催化剂的方法进行浮选硫泡沫,这对脱硫液的氧化能力影响很大,副盐的增长速率很高。
Many enterprises ignore the management in this regard and think that as long as the total amount of added salt remains unchanged, the growth rate of by-product salt has little to do with the way of addition. Some enterprises even flotation sulfur foam through the method of sudden addition of catalyst, which has a great impact on the oxidation capacity of desulfurization solution, and the growth rate of by-product salt is very high.
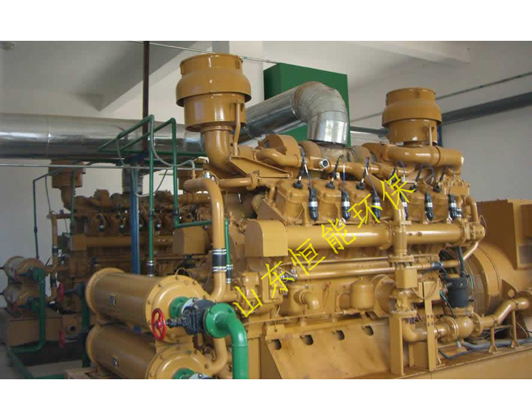
2、脱硫液成份的管理
2. Management of desulfurization liquid components
脱硫液成份不仅仅关系到脱硫效率和消耗的高低,同时也能反映出脱硫装置在生产运行中存在的问题,因此可以说,脱硫的工艺管理主要是脱硫液成份的管理。
The composition of the desulfurization liquid not only affects the efficiency and consumption of desulfurization, but also reflects the problems that exist in the production and operation of the desulfurization device. Therefore, it can be said that the process management of desulfurization mainly involves the management of the composition of the desulfurization liquid.
在脱硫液成份中对总碱度的认识有的企业还存在误区,认为只要总碱度达到指标就可以,却忽视了总碱度中碳酸钠的含量,实际总碱度是由碳酸钠和碳酸氢钠共同的决定的,脱硫液成份中应尽量提高Na2CO3含量,降低NaHCO3/ Na2CO3比值。在许多的焦化企业脱硫液中不分析硫酸铵的含量,这也给生产指导、事故判断带来一定影响。还有的企业对溶液的PH分析不重视,随便用PH试纸一测,误差很大,根本没有参考价值。
Some enterprises still have misconceptions about the understanding of total alkalinity in the composition of desulfurization solution, thinking that as long as the total alkalinity reaches the target, it is enough, but they ignore the content of sodium carbonate in the total alkalinity. The actual total alkalinity is determined by the combination of sodium carbonate and sodium bicarbonate. Therefore, the Na2CO3 content should be increased as much as possible in the composition of desulfurization solution, and the NaHCO3/Na2CO3 ratio should be reduced. In many coking enterprises, the content of ammonium sulfate is not analyzed in the desulfurization solution, which also has a certain impact on production guidance and accident judgment. Some companies do not attach great importance to the pH analysis of solutions and use pH test strips to measure them casually, resulting in significant errors and no reference value at all.
作为脱硫的技术管理人员应建好脱硫液成份台帐,从细节入手,健全分析项目,时刻关注溶液成份的变化趋势,明确变化的原因,才能正确判断脱硫系统是否存在问题,才能及时找出解决问题的办法,避免脱硫工艺恶化,防止脱硫工艺事故的发生。
As a technical manager of desulfurization, it is necessary to establish a ledger of the composition of the desulfurization liquid, start from details, analyze the project comprehensively, constantly pay attention to the trend of changes in the solution composition, clarify the reasons for changes, in order to correctly judge whether there are problems in the desulfurization system, find solutions in a timely manner, avoid the deterioration of the desulfurization process, and prevent the occurrence of desulfurization process accidents.
3、硫回收的管理
3. Management of sulfur recovery
硫回收率是判断脱硫系统运行是否正常的一个重要指标。对硫磺回收的管理各企业做的也大不一样,有的企业管理较好,有的企业管理较差。
The sulfur recovery rate is an important indicator to determine whether the desulfurization system is operating normally. The management of sulfur recovery varies greatly among enterprises, with some having better management and others having poorer management.
在硫回收的管理上主要是硫泡沫的浮选、熔硫釜的操作及废液的回收利用等问题。
The management of sulfur recovery mainly includes the flotation of sulfur foam, the operation of sulfur melting kettle and the recovery and utilization of waste liquid.
有的企业对硫泡沫的浮选不重视,尤其是夜班监控不到位,经常出现夜班硫磺回收率低的现象,有的企业甚至出现长时间硫磺回收率低的问题,管理人员也不管不问,也不组织职工查找原因,能出多少算多少,也不管硫磺回收率多少,这样脱硫系统出现问题也不能及时发现,到出现堵塔才查原因就有点晚了。
Some enterprises do not pay attention to the flotation of sulfur foam, especially the night shift monitoring is not in place, and the phenomenon of low sulfur recovery rate often occurs in the night shift. Some enterprises even have the problem of low sulfur recovery rate for a long time, and the management personnel do not ask or organize the staff to find out the reason, and the amount can be counted regardless of the sulfur recovery rate, so that problems in the desulfurization system can not be found in time, It's a bit late to investigate the cause until there is a tower blockage.
有的企业对熔硫釜的操作不重视,温度、压力控制不到位,清液中夹带的硫颗粒较多。有的企业在废液回收方面不进行降温、沉降处理就返回脱硫系统。
Some enterprises do not attach importance to the operation of sulfur melting kettles, and do not control the temperature and pressure properly, resulting in a large amount of sulfur particles carried in the clear liquid. Some companies return to the desulfurization system without cooling or settling treatment in waste liquid recovery.
当然大部分企业都非常重视硫回收工作,在管理方面做得了细化考核,能对各班组的硫磺产量进行计量,并根据各项指标进行考核,出现异常情况能及时查找原因。
Of course, most enterprises attach great importance to sulfur recovery work and have conducted detailed assessments in management. They can measure the sulfur production of each team and assess it based on various indicators. In case of abnormal situations, they can promptly identify the reasons.
4、生产过程的控制(硫泡沫的浮选、循环量、温度、压力、设备运行状况等)
4. Control of production process (flotation of sulfur foam, circulating volume, temperature, pressure, equipment operation, etc.)
在工艺管理中对熔硫后残液处理与回收工作也非常重要,对残液的处理一定要做到降温、静止沉降,分离副盐后取上层清液返回系统。沉降池要及时清理,保证残液有足够的降温、沉降空间。确保返回系统的清液质量合格,这一点也要引起脱硫工艺管理人员的重视。
The treatment and recovery of residual liquid after sulfur melting is also very important in process management. The treatment of residual liquid must achieve cooling, static settling, separation of secondary salts, and taking the upper clear liquid back to the system. The settling tank should be cleaned in a timely manner to ensure that there is sufficient cooling and settling space for the residual liquid. Ensure that the quality of the clear liquid returned to the system is qualified, which should also be taken seriously by desulfurization process management personnel.
This article is organized and published by biogas desulfurization. Do you have any understanding of these contents? For more information, please click on: https://www.hneee.net We will have more exciting content waiting for you to check out.