氩馏分从上塔抽出后,进入粗氩塔用精馏法进行氧、氩分离。一般粗氩塔顶引出的粗氩组分为:氩大于98%、氮小于0.5%、氧小于1.5%。将纯度大于98%的粗氩导入分子筛吸附器。每组吸附器设置2台,一台吸附器内装5A分子筛,吸附粗氩气中的氮;另一台吸附器内装4A分子筛,吸附粗氩气中的氧。
After the argon fraction is extracted from the upper tower, it enters the crude argon tower for oxygen and argon separation using distillation method. Generally, the components of coarse argon extracted from the top of the coarse argon tower are: argon greater than 98%, nitrogen less than 0.5%, and oxygen less than 1.5%. Introduce crude argon with a purity greater than 98% into the molecular sieve adsorber. Two adsorbers are set for each group, with one adsorber containing 5A molecular sieve to adsorb nitrogen from coarse argon gas; Another adsorber is equipped with 4A molecular sieve to adsorb oxygen from crude argon gas.
为了吸附剂的解吸,吸附器需要设置两组,切换使用。吸附器在90K温度条件下工作,粗氩气入5A分子筛吸附器除氮,然后进入4A分子筛吸附器除氧,其流程见图18。从一组分子筛吸附器出来的气体含氩纯度可达到99.99%,即为纯氩。
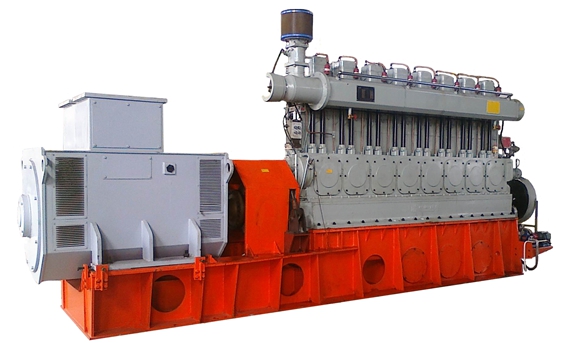
In order to desorb the adsorbent, two sets of adsorbers need to be set up and switched for use. The adsorber operates at a temperature of 90K. The coarse argon gas first enters the 5A molecular sieve adsorber for nitrogen removal, and then enters the 4A molecular sieve adsorber for oxygen removal. The process is shown in Figure 18. The gas from a group of molecular sieve adsorbers can have an argon purity of 99.99%, which is pure argon.
吸附法制氩的优点在于,工艺流程简单、操作方便、成本低。但是,氩的纯度只能达到99.99%。由于受分子筛选择吸附能力的限制,无法获得纯度为99.999%。A的高纯氩气。另一个缺点是,吸附器的工作温度为90K,再生温度为423K,吸附结构设计较为困难。
The advantages of adsorption method for argon are simple process flow, convenient operation, and low cost. However, the purity of argon can only reach 99.99%. Due to the limitation of the selective adsorption capacity of molecular sieves, a purity of 99.999% cannot be obtained. A's high-purity argon gas. Another disadvantage is that the working temperature of the adsorber is 90K, and the regeneration temperature is 423K, making the design of the adsorption structure more difficult.
吸附器工作时,床层必须冷却,往往需采用夹套或管内通液氧冷却。若想达到均一的冷却温度,对于大型制氩设备所需直径较大的吸附器来说,就十分困难。因为有以上两个缺点,限制了吸附法制纯氩的应用。目前,国内吸附法制氩能力不超过10m3/h,只在150m3/h空分设备配套的制氩设备上采用,在大型制氩设备上尚无应用。
When the adsorber is working, the bed layer must be cooled, often using a jacket or liquid oxygen cooling inside the tube. It is very difficult to achieve a uniform cooling temperature for larger diameter adsorbers required for large-scale argon production equipment. Due to the above two drawbacks, the application of adsorption method for pure argon is limited. At present, the adsorption method for argon in China has a capacity of no more than 10m3/h and is only used on argon production equipment matched with 150m3/h air separation equipment. It has not yet been applied to large-scale argon production equipment.